Top Quality Packaging Machine Repair Service to Maximize Manufacturing Efficiency
Top Quality Packaging Machine Repair Service to Maximize Manufacturing Efficiency
Blog Article
Vital Considerations for Fixing and Repairing Your Packaging Machine
When attending to the intricacies of troubleshooting and repairing your product packaging device, several critical aspects need to be taken into consideration to guarantee both effectiveness and safety. What various other essential components could be the trick to boosting your maker's reliability?
Recognizing Usual Issues
Recognizing usual issues in product packaging makers is essential for maintaining operational effectiveness and minimizing downtime. Packaging devices, integral to production lines, can experience a selection of problems that impede their efficiency. One prevalent concern is mechanical breakdown, frequently arising from deterioration on components such as belts and gears, which can bring about irregular product packaging quality.
Another typical issue is misalignment, where the packaging products might not line up properly, causing jams or improper sealing. This imbalance can originate from incorrect arrangement or adjustments in material specs. In addition, electric failings, such as damaged sensors or control systems, can interrupt the equipment's automated processes, bring about production hold-ups.
Operators may also experience challenges with software program problems, which can affect device programs and capability. Inadequate maintenance techniques usually contribute to these issues, highlighting the need for regular assessments and timely solution interventions. By understanding these typical problems, operators can implement proactive steps to make certain peak efficiency, thereby lowering pricey downtimes and boosting total efficiency in product packaging operations.

Diagnostic Tools and Strategies
Reliable troubleshooting of packaging makers depends greatly on a range of analysis tools and methods that promote the identification of underlying problems - packaging machine repair service. One of the key tools is making use of software program diagnostic programs, which can monitor device performance, assess error codes, and give real-time data analytics. These programs make it possible for specialists to determine particular malfunctions swiftly, significantly lowering downtime
In addition to software application oscilloscopes, options and multimeters are necessary for electrical diagnostics. Multimeters can measure voltage, present, and resistance, aiding to recognize electric faults in circuits. Oscilloscopes, on the other hand, provide visualization of electric signals, making it less complicated to identify irregularities in waveforms.
Mechanical issues can be identified utilizing vibration analysis devices and thermal imaging video cameras. Vibration analysis enables for the detection of discrepancies or misalignments in equipment, while thermal imaging helps identify overheating parts that may cause mechanical failure.
Finally, aesthetic examinations, incorporated with common checklists, continue to be very useful for standard troubleshooting. This detailed method to diagnostics guarantees that professionals can effectively address a broad array of issues, thereby boosting the reliability and efficiency of packaging devices.
Safety Procedures to Comply With
Exactly how can packaging device drivers guarantee a safe workplace while repairing? The application of rigorous security methods is essential. Operators must begin by disconnecting the device from its power resource prior to starting any troubleshooting procedures. Lockout/tagout (LOTO) methods must be imposed to stop unexpected re-energization during upkeep.

Operators needs to additionally familiarize themselves with the machine's security attributes, such as emergency quit buttons and safety and security guards, verifying that they are useful before beginning any kind of diagnostic work. packaging machine repair service. It is essential to interact with staff member, making certain all employees are conscious of the recurring troubleshooting activities
Last but not least, drivers ought to record all findings and procedures, supplying a clear record in instance of future concerns. By sticking to these security procedures, packaging equipment operators can create a more secure atmosphere, reducing dangers while effectively troubleshooting and fixing equipment.
Parts Substitute Guidelines
When it involves keeping product packaging makers, recognizing components substitute guidelines is important for making certain optimum efficiency and long life. Consistently analyzing wear and tear on machine elements is critical, as prompt replacements can protect against extra extensive damage and expensive downtime.
To start with, always refer to the maker's requirements for recommended substitute intervals and component compatibility. It is necessary to use OEM (Original Equipment Supplier) components to guarantee that replacements meet the required high quality and performance criteria.
Before beginning any substitute, ensure the equipment is powered down and effectively shut out to prevent accidental activation. Record the condition of the changed parts over at this website and the date of substitute, as this will assist in monitoring upkeep patterns in time.
Furthermore, examine the bordering elements for indications of wear or potential concerns that might arise from the substitute. This holistic technique can minimize future problems and improve functional performance.
Finally, after changing any type of parts, conduct detailed testing to make sure that the equipment is functioning correctly which the new elements are incorporated perfectly. Adhering to these standards will certainly not only extend the life of your packaging machine however likewise enhance total productivity.
Upkeep Best Practices
Consistent upkeep methods are essential for making best use of the effectiveness and life-span of product packaging equipments. Establishing a detailed upkeep schedule is the initial step toward making sure optimum efficiency. This routine ought to consist of daily, weekly, and monthly tasks tailored to the particular machine and its operational demands.
Daily checks ought to focus on important elements such as seals, belts, and sensing units, guaranteeing they are tidy and functioning correctly. Weekly upkeep may involve examining lubrication levels and tightening loose installations, while month-to-month tasks need to consist of a lot more thorough examinations, such as alignment checks and software program updates.
Making use of a checklist can simplify these processes, making certain no crucial tasks are neglected. In addition, maintaining exact documents of upkeep tasks helps identify repeating issues and informs future techniques.
Training staff on correct use and handling can significantly decrease deterioration, avoiding unnecessary break downs. In addition, investing in top notch parts and lubes can boost device efficiency and reliability.
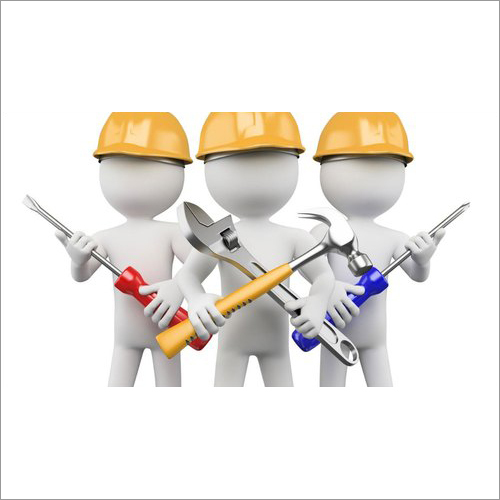
Final Thought
To conclude, reliable fixing and repair service of packaging devices require a structured strategy encompassing safety protocols, making use of suitable analysis tools, and adherence to upkeep finest techniques. Timely components and routine evaluations substitute with OEM elements play a critical function in maintaining maker efficiency and integrity. Thorough documentation of procedures and findings contributes to a deeper understanding of recurring issues, inevitably enhancing functional effectiveness and reducing the possibility of future malfunctions.
When dealing with the complexities of troubleshooting and fixing your packaging maker, numerous essential variables have to be considered to make certain both efficiency and safety and security.Recognizing typical problems in packaging equipments is important for maintaining functional efficiency and lessening downtime.Efficient troubleshooting of product packaging equipments counts heavily on a selection of analysis devices and techniques that facilitate the recognition of underlying problems.Exactly how can product packaging machine operators guarantee a safe functioning environment Source while fixing?In verdict, reliable troubleshooting and repair service of product packaging equipments necessitate an organized technique encompassing security procedures, the use of proper diagnostic tools, and adherence to maintenance best practices.
Report this page